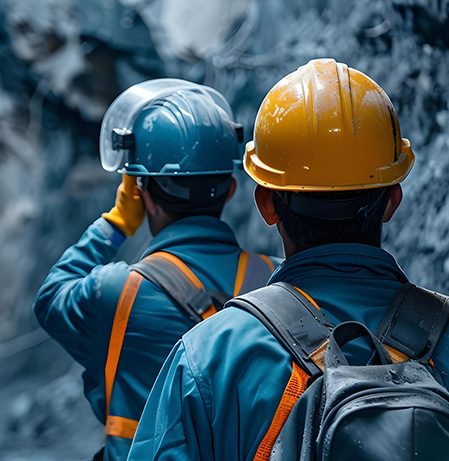
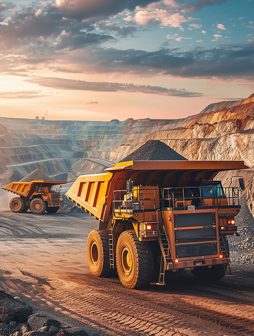
OPERATIONAL SERVICES
UMOYA VOHE Solutions can provide Operational Services comprising of but not limited to:
- Staffing of qualified vent / occupational hygiene departments (part/full time)
- Carrying of legal appointments (part/full time)
- Workplace Monitoring and Surveys
- Section 11.5 Investigations on any Health Threatening Occurrence
- Statistical Analysis of annual exposure data
- Development and Implementation of Occupational Hygiene Programs
COMPILATION / REVISION OF
Mandatory Code of Practices in accordance with the latest guidelines.
- Mandatory Code of Practice for an Occupational Health Programme for Noise
- Mandatory Code of Practice for an Occupational Health Programme on Personal Exposure to Airborne Pollutants
- Mandatory Code of Practice for an Occupational Health Programme on Thermal Stress
- Mandatory Code of Practice for the Prevention of Flammable Gas Explosions in Mines other than Coal Mines
- Mandatory Code of Practice on Minimum Standards of Fitness to Perform Work
- Mandatory Code of Practice on Emergency Preparedness and Response
- Mandatory Code of Practice for Fatigue Management
- Mandatory Code of Practice for Prevention of Fire at Mines
- Mandatory Code of Practice on Women in Mining
- Mandatory Code of Practice for a Quality Assurance Programme for a System of Occupational Hygiene and Ventilation Engineering Measurements
LEGAL
REPORTING SOFTWARE
UMOYA has developed an Occupational Hygiene Management and Reporting Software dedicated to provide an all-inclusive platform for legal reporting to the DMRE which includes:
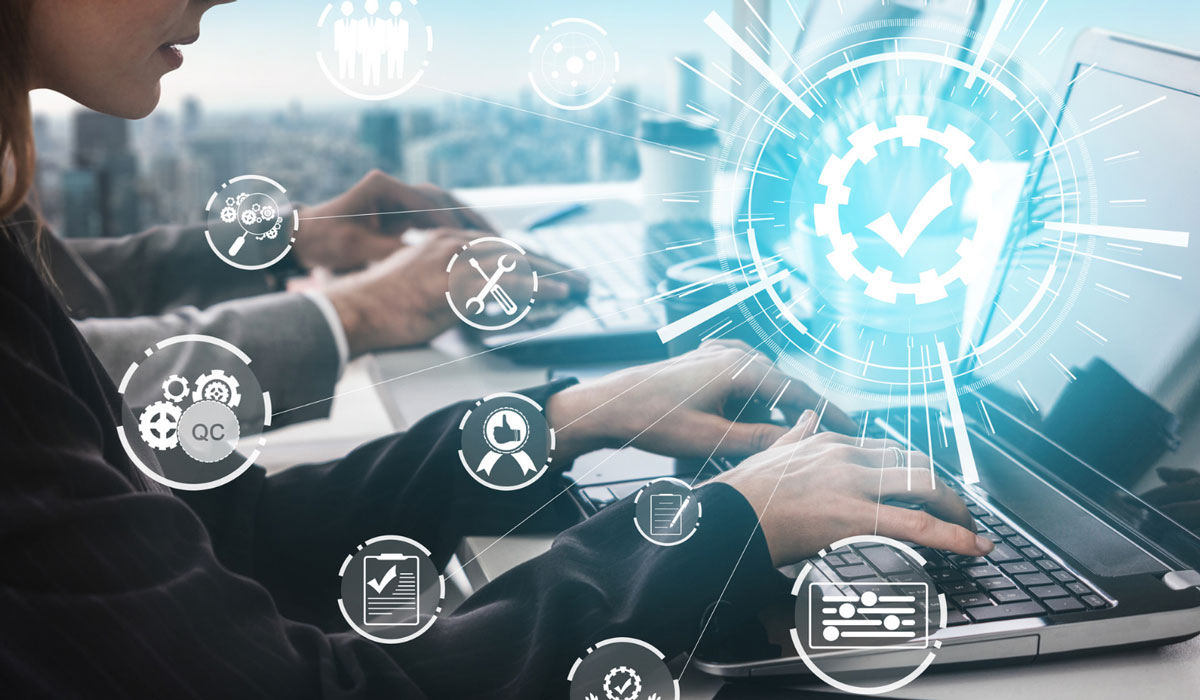
Compilation of Mandatory DMR Reports
- Operation Details Report Form
- Particulates Personal Exposure Report Form 21.9(2)(a)
- Additive Pollutants
- Single Pollutants
- Gases and Vapours
- Personal Noise Exposure Report Form 21.9(2)(e)
- Noise and Silicosis Milestones Report
Populating Sampling Strategy based on
- Historical personal exposure data – 90th percentile exposures of employees in HEG for previous sampling period
- Number of employees assigned to the specific HEG
- Risk Classification according to guideline
Equipment register setup
- Equipment Description
- Equipment Type
- Serial Number
- OEM
- Calibration Dates
- Calibration Certificates – uploaded onto the system as proof
Flagging and Control System
- Email notification to alert user when an instrument is due for calibration.
- Email notification to alert end user that there is an over-exposure that needs to be investigated and actioned.
- System will not allow an instrument to be selected if instrument falls outside calibration specifications.
- System will not save an exposure result if the runtime and flowrates does not fall within specification – pre setup as per client requirements
RISK
ASSESSMENTS
Specialized Occupational Hygiene Risk Assessments focus on identifying and evaluating health hazards in the workplace that can affect workers’ health over time. These risks are typically related to exposure to harmful substances, conditions, or processes that might not cause immediate harm but could lead to chronic health problems. Occupational hygiene is primarily concerned with controlling risks associated with chemical, physical, biological, and ergonomic hazards. Specialized risk assessments often take into account factors such as the nature of the exposure, how it occurs, and the duration and frequency of contact.
Key Components of Specialized Occupational Hygiene Risk Assessments:
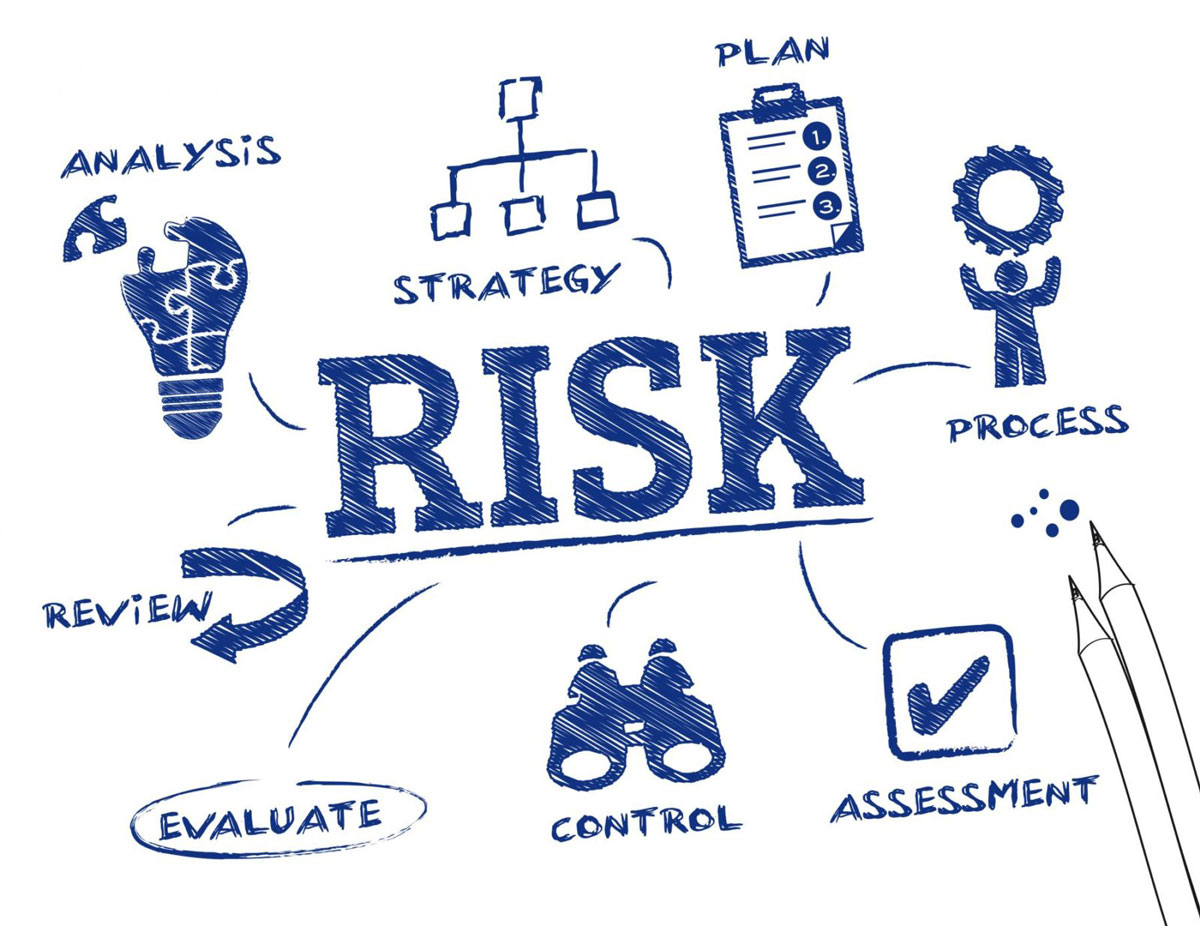
Hazard Identification
- Chemical hazards: Exposure to toxic substances like solvents, metals, or fumes.
- Physical hazards: Risks related to noise, vibration, temperature extremes, radiation, or poor lighting.
- Biological hazards: Exposure to bacteria, viruses, molds, or allergens in the workplace.
- Ergonomic hazards: Repetitive strain injuries, awkward postures, and unsafe manual handling practices.
Exposure Assessment
- Monitoring: Collecting data on worker exposure levels using air sampling, noise measurements, or biological monitoring.
- Workplace surveys: Observing and recording the conditions under which work is performed, including the processes, equipment used, and work environments.
- Personal monitoring: Using devices such as dosimeters or sensors that track a worker’s exposure to hazards in real-time.
Risk Evaluation
- Toxicological data: Reviewing data on the harmful effects of substances and conditions, including exposure limits and health risks.
- Health surveillance: Reviewing medical records or conducting pre-employment and periodic health checks to track long-term effects.
- Control measures: Evaluating the effectiveness of current engineering controls (ventilation, containment), administrative controls (schedules, training), and personal protective equipment (PPE).
Control Recommendations
- Engineering Controls: Modifying equipment, processes, or systems to minimize exposure. For example, installing fume hoods, soundproofing, or improving ventilation.
- Administrative Controls: Adjusting work practices, rotating workers, limiting exposure time, or providing breaks to reduce health risks.
- PPE: Providing workers with appropriate personal protective equipment such as respirators, gloves, or ear protection.
Documentation and Review
- Reporting: Creating detailed reports summarizing the findings, risks, and recommended actions.
- Follow-up: Ensuring that the implemented control measures are working effectively through ongoing monitoring, audits, and assessments.
Examples of Specialized Risk Assessments
- Asbestos exposure assessments: Identifying risks in industries where workers may be exposed to asbestos fibers, such as construction, demolition, or insulation work.
- Noise exposure assessments: For environments with high noise levels (factories, airports), evaluating the risk of hearing damage or loss.
- Chemical exposure assessments: For laboratories or manufacturing plants handling hazardous chemicals, such as paints, solvents, or pesticides.
CONFINED
SPACES
A confined space refers to a space that is not designed for continuous human occupancy but may be large enough for a person to enter and perform work. These spaces typically have restricted entry or exit, and they may pose risks due to hazardous conditions or limited ventilation.
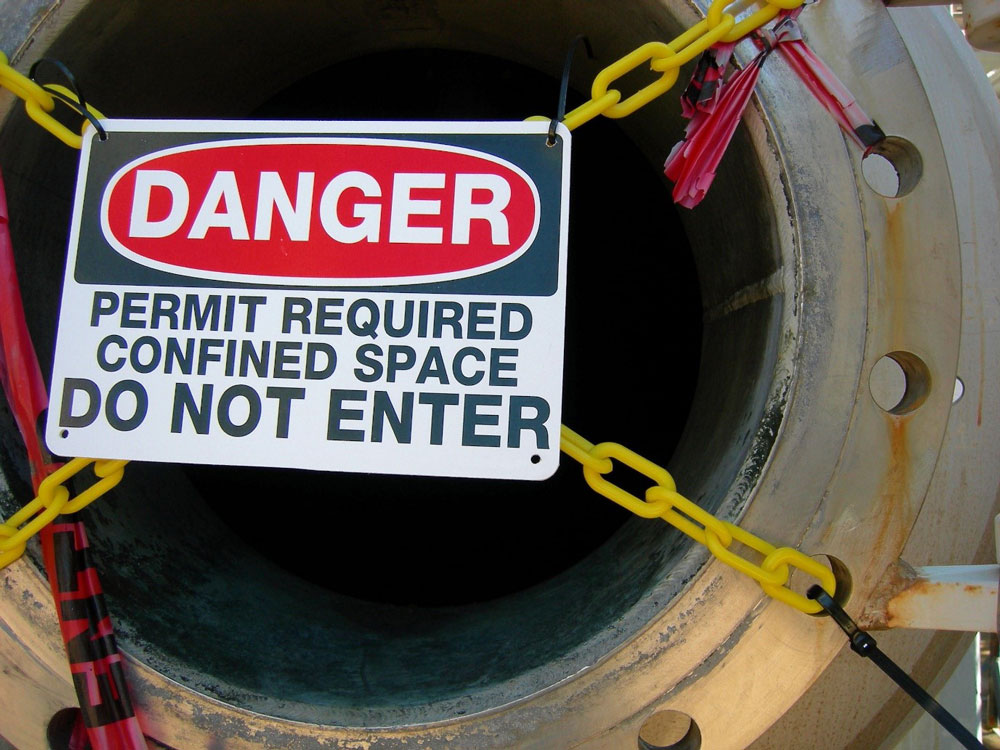
Key Characteristics of Confined Spaces
- Limited entry or exit: The space is difficult to access or exit due to size or design constraints.
- Not intended for continuous occupancy: The space is not meant for people to work in regularly or for long periods.
- Potential for hazardous atmosphere: There may be poor ventilation, lack of oxygen, or the presence of toxic gases, vapours, or fumes.
- Risk of physical hazards: These spaces may have the potential for entrapment, falling objects, or equipment that could pose a danger to workers.
Common Examples of Confined Spaces
- Tanks, silos
- Sewers and pipelines
- Boilers, furnaces, and chimneys
- Pits, vaults, and crawl spaces
- Storage bins and hoppers
Hazards Associated with Confined Spaces
- Atmospheric hazards: These can include oxygen deficiency, toxic gases (such as carbon monoxide or hydrogen sulphide), or flammable gases.
- Physical hazards: Such as mechanical equipment, insufficient illumination, uneven surfaces, or the potential for being trapped or engulfed.
- Engulfment hazards: Materials like grain, sand, or liquid could pose a risk of engulfment or suffocation.
- Temperature extremes: High or low temperatures may pose risks of heat stress or cold-related injuries.
Testing must be done by competent personnel using calibrated instruments. Continuous monitoring may be necessary during entry.
Clearance for work in confined spaces must be managed by competent personnel. These personnel must ensure that confined spaces are safe to enter by performing necessary risk assessments, conducting atmospheric testing, issuing entry permits, and preparing rescue plans. Their role is critical in ensuring that confined space work is performed safely and in compliance with the MHSA regulations to protect the health and safety of workers.
UMOYA can provide an all-inclusive service related to confined spaces
- Atmospheric testing performed by competent personnel;
- Training with regard to clearance, gasses and ventilation;
- Specialised Clearance with regards to Hot Work, Lead (Pb), Asbestos, HEPA filters;
- Ventilation requirements;
- Confined Space Risk Assessments;
- Supply of specialised equipment
- Gas Detection Instruments;
- Fans (Force and or Exhaust);
- Ducting;
- Fan monitoring device;
- Gas monitoring device;
- Recirculation of expelled air through HEPA filter systems (Lead and or asbestos)
VENTILATION
& REFRIGERATION
- Design and Planning
- Modelling and software development for mine ventilation and cooling systems;
- Conceptual investigations, pre-feasibility and feasibility design studies and implementation;
- New mine / project design;
- Expansion design for existing mine ;
- Shaft sinking design;
- Industrial design, Laboratory extraction system
- Turn-key project execution and management (design, install, commission, operate);
- Verification audits by means of measurements (performance testing of ventilation and refrigeration systems).
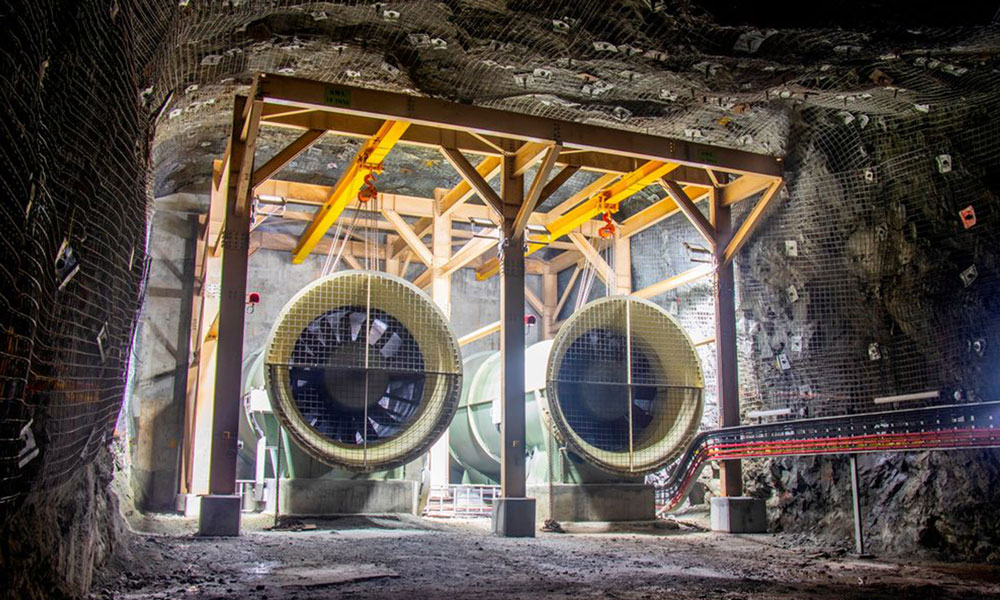